Secrets de fabrication : la FSTT envoie ses meilleurs espions en Allemagne !
82 kilomètres séparent le Palais des Congrès de Strasbourg de la petite bourgade de Rohrbach, en Allemagne.
Le premier accueillait mardi 18 octobre 2022 la Journée des Techniques Sans Tranchée du Grand Est. La seconde accueille depuis 2009 le siège et l’usine de fabrication de RelineGroup, comptant désormais 6 entités partout sur le globe.
Profitant donc de sa présence sur place et portée par l’aimable invitation de David Veltz, directeur commercial France & Belgique, toute l’équipe de la FSTT est allée vérifier in-situ si la Deutsche Qualität était toujours ce qu’elle était.
C’est ainsi qu’une délégation d’une petite dizaine de personnes a pris plaisir à découvrir, à travers une visite fort instructive, certains petits secrets de fabrication du fabricant de l’Alphaliner, gaine permettant la réhabilitation sans tranchée de conduites d’assainissement souterraines par gonflage puis polymérisation aux UV.
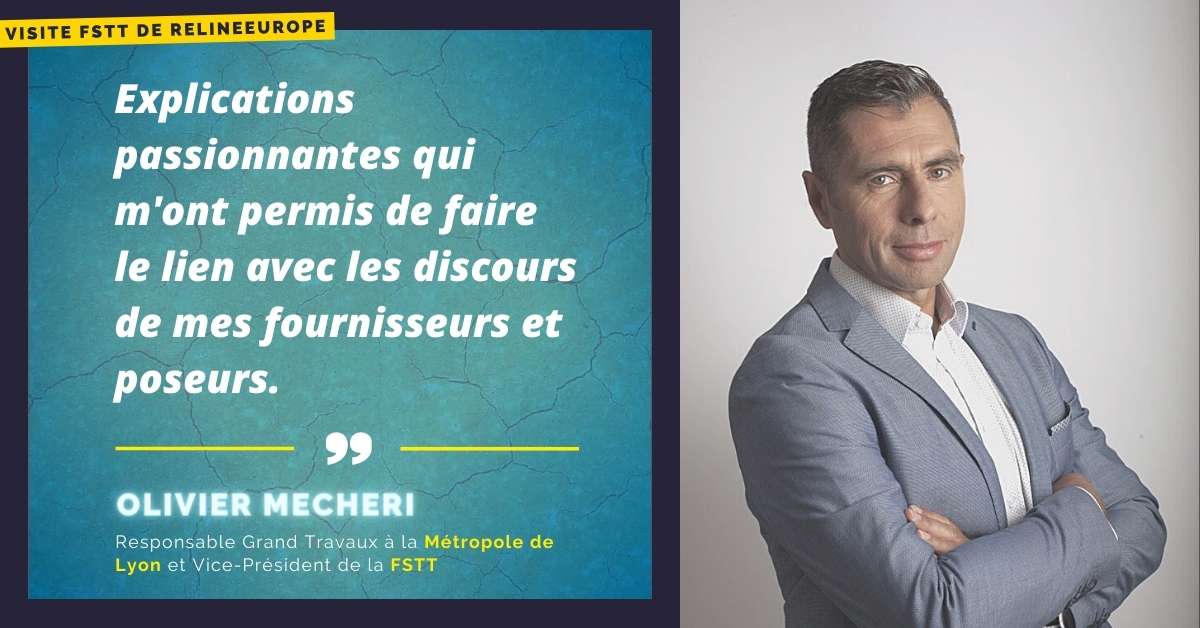
On a percé le secret !
Cette visite a notamment faire ressortir un engagement fort autour de 3 piliers :
- Une qualité “totale”
- Un lien étroit avec ses partenaires poseurs
- Une prise en compte globale des enjeux environnementaux.
Découverte de ce cercle vertueux.
Zoom sur la réhabilitation sans tranchée par chemisage continu polymérisé en place par UV
La réhabilitation des réseaux d’assainissement, un enjeu urgent !
La réhabilitation des conduites d’assainissement constitue un défi majeur pour les acteurs publics et privés. Toutes les analyses du taux de remplacement de notre réseau d’assainissement mettent en évidence le faible niveau de priorité qui lui est consacré.
Dans quasiment toutes les agglomérations et métropoles, on voit que le taux de renouvellement est très faible par rapport à ce qu’il devrait être.
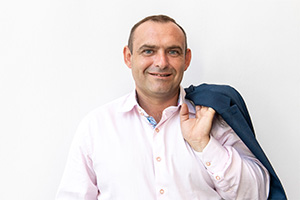
Souvent considéré comme le « parent pauvre » de la gestion patrimoniale, le renouvellement de l’assainissement souffre d’un investissement public en baisse constante et d’une attention davantage portée sur les programmes de réfection de voirie.
Moins onéreuse que le renouvellement, la réhabilitation des réseaux d’assainissement vieillissants gagne les faveurs de collectivités.
Il existe toutefois de nombreuses techniques de réhabilitation. Pour les départager, seul le triptyque « évaluation / diagnostic / préconisation » est à même d’assurer le bon choix au meilleur coût, mais aussi dans la maîtrise de la gêne occasionnée et des nécessités environnementales.
Temps, argent et CO2 : le chemisage UV, idéal pour les collectivités qui veulent le beurre et l’argent du beurre !
La réhabilitation par chemisage ne nécessite aucune tranchée, pas même de création de puits : la gaine souple comportant une couche de fibre de verre thermodurcissable est introduite dans la canalisation existante en passant par les regards de visite, puis gonflée et finalement polymérisée par un train de lampes UV, créant ainsi une canalisation « neuve » à l’intérieur de l’ancienne.
Vidéo explicative du chemisage continu par polymérisation aux ultraviolets 👇
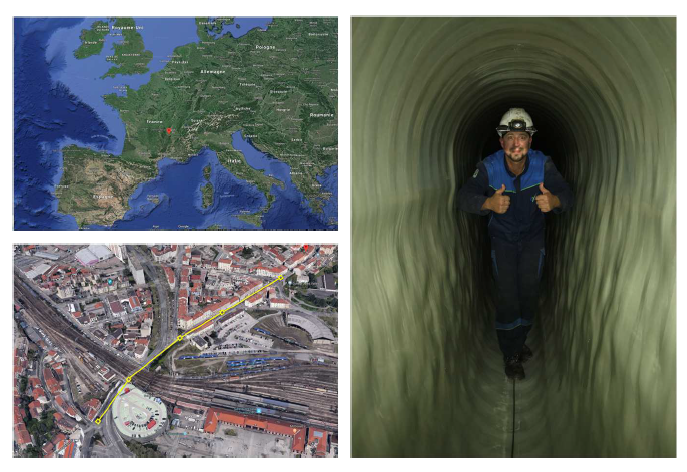
Annoncé pour une durée de vie de 50 ans minimum, au même titre qu’un ouvrage neuf, et ne comportant aucun joint, ce procédé apporte de sérieux avantages.
« Notre technique permet de gagner du temps avant tout » estime David Veltz.
Elle permet effectivement de poser de grandes longueurs – jusqu’à 600 mètres en un seul morceau – sur tous types de diamètres et de profils (circulaire, ovoïde et en arche), dans un délai extrêmement court. Le tout sur un diamètre nominal de 150 à 2000 mm.
Mais ça n’est pas là son seul avantage. Cette méthode permet très souvent de générer des économies, et son coût environnemental s’avère sans commune mesure avec une réhabilitation par des techniques dîtes « conventionnelles », ces dernières entrainant d’importantes quantités de gravats à évacuer ainsi qu’une réfection complète des enrobés après les travaux.
Émissions de CO² et nuisances auprès des riverains sont ainsi considérablement réduites.
Pour ces différentes raisons, la technique sans tranchée de réhabilitation par chemisage d’une gaine polymérisée aux UV est particulièrement utilisée par les grandes sociétés en France – la SNCF, les aéroports, EDF – et bien entendu dans le domaine public.
Les 3 facteurs clés de succès de Reline Europe
1. Vers une qualité « totale »
Présente dans l’ADN de l’entreprise dès sa création, l’assurance qualité s’est renforcée davantage encore en 2020 chez RelineEurope. Cette année-là, qui marque également un changement de Direction, le fabricant de gaine Allemand lance officiellement la démarche TQM, pour Total Quality Management.
Bien connue en Allemagne, notamment dans le milieu automobile, la démarche TQM est particulièrement impliquante pour le fabricant, qui s’impose ainsi des contrôles manuels ou automatiques à chacune des étapes, de l’entrée des matières premières à la documentation des données sur le chantier final.
Le tout est méticuleusement documenté et consigné, permettant de réagir partout dans le monde en cas de nécessité.
Une démarche de qualité facilitée par le fait que RelineEurope maîtrise l’intégralité de la chaîne de production, depuis la fabrication de l’une de ses matières premières jusqu’au système de polymérisation par train de lampes à ultraviolet, qu’il conçoit et qu’il fournit à ses partenaires poseurs.
2. Un lien étroit et constant avec ses applicateurs
Le second facteur contribuant au rayonnement mondial du fabricant découle directement du 1er : à quoi bon délivrer un produit, aussi parfait soit-il, si ceux qui en assurent la mise en place pour le client final ne maîtrisent pas le process sur le bout des doigts ?
C’est ainsi qu’est née l’idée de la RelineAcademy.
C’est le partenariat avec nos applicateurs qui est important, car c’est l’applicateur qui va finir le produit. Nous avons donc besoin de faire valoir notre cahier des charges jusqu’à la pose définitive.
Cette formation peut s’allonger sur une durée initiale de 6 à 12 mois, et se prolonge ensuite en continu, à mesure des évolutions des produits, des techniques mais aussi des besoins des poseurs. « Un applicateur doit toujours rafraichir ses formations » confirme David Veltz. Ses besoins seront différents selon ses chantiers, ses clients, ses secteurs d’activité, etc.
Les techniciens peuvent se former chaque année au titre de la RelineAcademy, le plus souvent possible dans leur langue maternelle avec un technicien attitré.
Pour assurer la continuité de sa démarche qualité jusqu’au produit final, le fabricant a mis en place la norme NF 390, marque de qualité qui lie le fabricant avec l’applicateur et qui permet d’avoir une traçabilité totale sur les process lors de sa mise en œuvre.
3. Une prise en compte globale des enjeux environnementaux
Enfin, le dernier pilier de croissance et d’attractivité de RelineEurope se trouve du côté de son engagement sociétal. Déjà au cœur de gains colossaux d’émissions de gaz à effet de serre et de nuisances diverses par le simple fait d’exploiter un procédé sans tranchée, l’entreprise a misé dès le début sur le cercle vertueux du développement durable.
Dès la conception de l’usine, l’aspect environnemental fut considéré avec une attention particulière, puisque 9 000 m² de panneaux solaires furent installés sur les toits de l’usine.
En complément, le process de fabrication a été conçu autour de la récupération d’une partie des matières premières non exploitée, le styrène. Ce dernier est récupéré puis brûlé, les calories dégagées permettant de chauffer le bâtiment. L’usine produit donc une partie de sa propre chaleur lorsqu’elle tourne.
En complément, la chaudière au fioul a été plus récemment remplacée au profit d’une chaudière à pellets, particulièrement utile pour les moments où l’usine est à l’arrêt lors des phases hivernales d’entretien.
Enfin, les nombreux voyages d’affaires de la force commerciales sont intégralement compensés en CO². Pour cela, la société s’appuie sur TravelPerk, société spécialisée dans le tourisme d’affaire durable, qui calcule les émissions produites, les « facture » à ses clients et investis les fonds récoltés dans des projets à impact certifiés partout dans le monde.
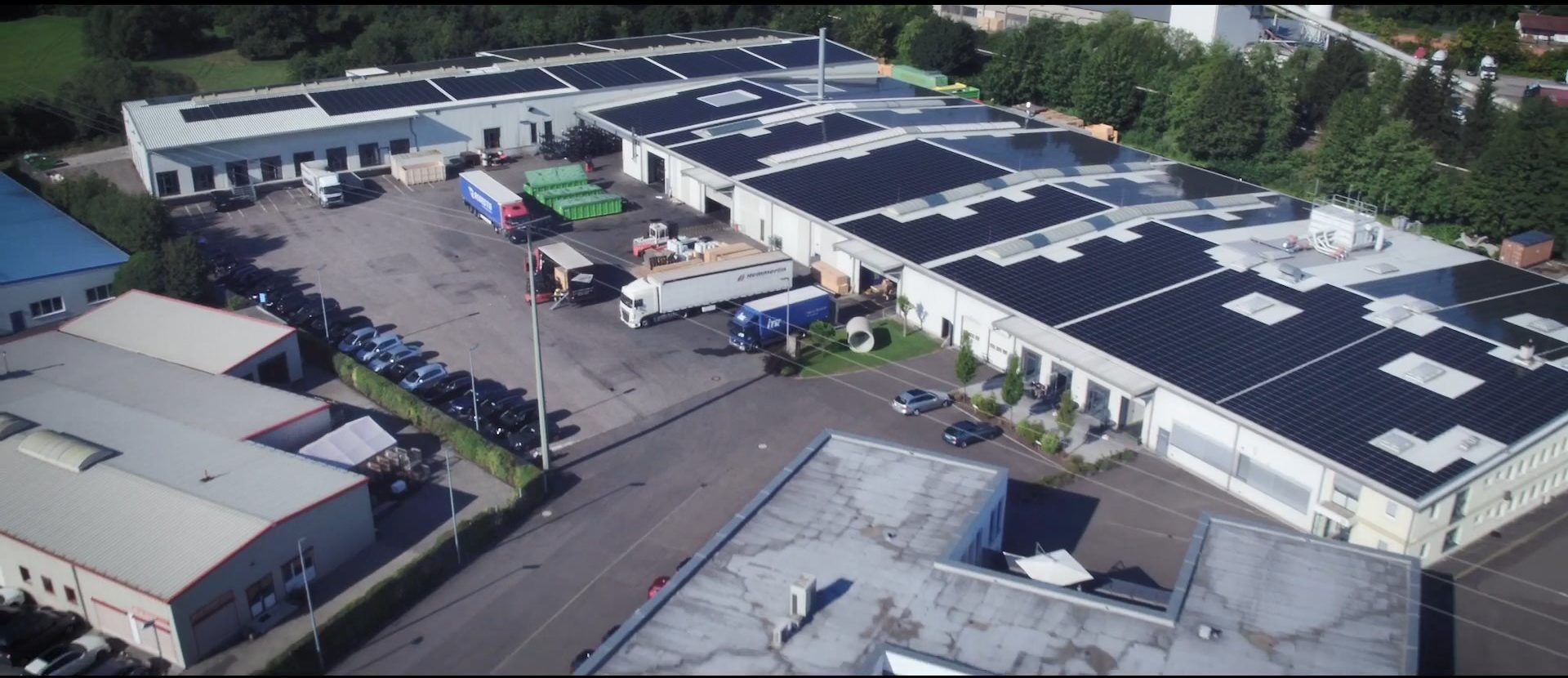
9 000 m² de panneaux solaires couvrent les toits de l’usine Reline Europe, à Rohrbach.
Voilà pour les actions déjà effectuées, mais le fabricant européen, dont les produits sont régulièrement posés dans des ZFE (Zones à Faible Emission), compte bien aller encore plus loin dans le cercle vertueux. Raison pour laquelle il consacre une bonne part de son budget R&D dans le développement de systèmes complètement électriques pour l’étape de polymérisation. Batteries ou raccordement au réseau électrique urbain viendront demain remplacer les génératrices actuelles (voir l’interview ci-dessous).
Interview : RelineEurope, un innovateur tourné vers l’avenir
FSTT. Vous n’êtes pas les seuls à produire des gaines polymérisables en UV. Est-ce qu’il y a quelque chose que vos concurrents ne possèdent pas ?
David Veltz. Ce qui nous différencie en premier lieu, c’est déjà le fait d’être un fournisseur global. On est aujourd’hui le seul fabricant à proposer le produit, la matière première et le système de polymérisation.
Etant fabricant de l’une de nos matières premières, nous maitrisons mieux la partie conception de notre produit, ce qui nous permet de l’optimiser plus facilement. Être moins tributaire des process d’approvisionnement s’inscrit également dans une garantie de livraison de nos produits auprès des applicateurs.
Notre second point de différenciation de nos confrères réside dans l’épaisseur de nos produits, puisqu’on est capable de fournir des gaines jusqu’à 30 mm, dont on garanti une polymérisation uniquement aux ultraviolets jusqu’à 20 mm. Ce qui apporte une stabilité avant mise en œuvre de 6 mois.
Comment voyez-vous l’avenir de votre métier ?
C’est dans l’assainissement gravitaire que l’on s’est spécialisé et développé, mais nous avons principalement deux axes de développement.
- Le 1er est d’investir le marché de l’eau potable. Nous sommes le premier fabricant français à obtenir un ACS* avec un produit polymérisé aux UV, pour lesquels plusieurs chantiers ont lieu en France.
(*Attestation de Conformité Sanitaire) - Le 2nd concerne le développement des produits du futur. Nous travaillons sur les premières gaines connectées, qui permettront de donner l’information au plus vite en cas de problème, sans passage de caméra, dans les environnements qui nécessitent un contrôle permanent de leurs installations.
Au-delà des gaines, nous travaillons également sur une méthode nous permettant de réduire encore davantage les nuisances dans les centres villes, et globalement dans tous les zones à faible émissions (ZFE). Pour cela, notre procédé étant électrique, on travaille sur un système qui ne passera pas par une génératrice, consommatrice de produits pétroliers.
Cela devrait voir le jour courant 2023 pour les petits diamètres grâce à des systèmes de batterie. Pour les gros diamètres, nous étudions la faisabilité de raccordement aux armoires électriques des réseaux urbains.
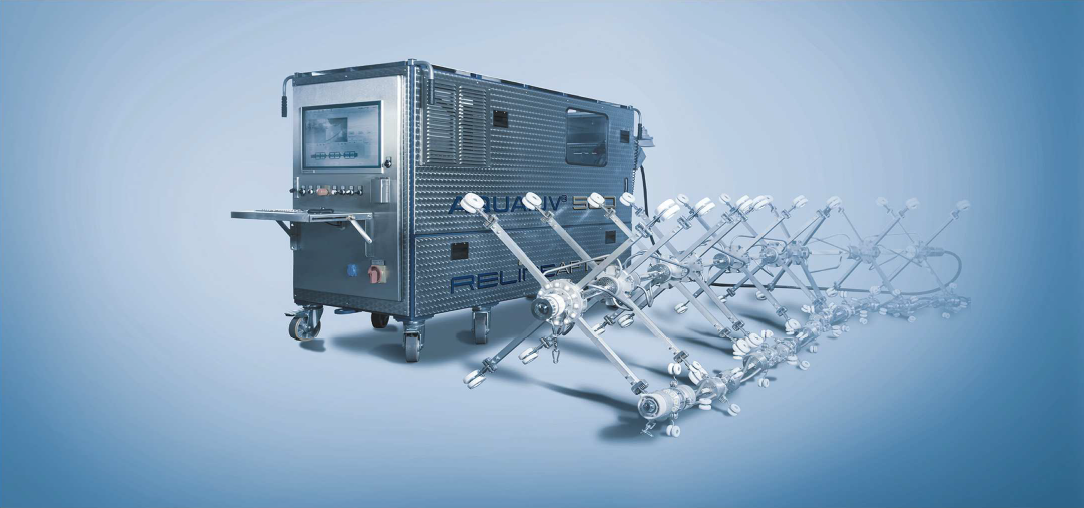
Comment percevez-vous la demande de travaux sans tranchée ?
La demande du sans tranchée est en progression, plus ou moins importante mais véritablement continue, notamment à l’international mais également en France.
« Il fut un temps ou notre production était saisonnière, car les chantiers ne s’effectuent pas en dessous de -5°. Mais notre demande étant aujourd’hui mondiale, on produit pratiquement tout le temps. »
David Veltz, Responsable Commercial France & Belgique chez RelineEurope
Vous participez à un projet remarquable ?
Innovation produit, technique novatrice, ampleur du chantier importante : la FSTT est là pour relayer vos exploits ! Que le chantier soit à venir ou déjà effectué, envoyez-nous toutes les informations utiles et nous le relayerons sur nos sites et nos réseaux.